Table of Contents
Liquid ring vacuum pumps are widely used in industries that require precise control of vacuum pressure. Their design, which utilizes a rotating liquid ring to trap and move gases, allows them to perform effectively in environments such as chemical processing, pharmaceuticals, food packaging and more. The internal components of these pumps play a critical role in determining their efficiency, reliability and overall performance. Understanding how these components-specifically the rotor, casing, seals and shaft assemblies-work together to create and maintain a vacuum is essential for optimizing the performance of liquid ring vacuum pumps.
In this guide, we’ll explore the internal components that influence liquid ring vacuum pump performance, focusing on how each part contributes to the pump’s overall functionality. We’ll also highlight the importance of these components in ensuring energy efficiency, reducing maintenance and increasing the lifespan of the pump.
How the Rotor Design Enhances the Efficiency of a Liquid Ring Vacuum Pump?
The rotor is the heart of any liquid ring vacuum pump. It is responsible for generating the necessary forces to displace air and create the vacuum. The rotor typically features an eccentric design and is positioned within the pump casing. As the rotor spins, it interacts with the liquid ring, creating the low-pressure environment essential for vacuum operation.
The design of the rotor significantly impacts the pump’s efficiency. A well-designed rotor can help maintain a consistent vacuum by ensuring that the gas is efficiently trapped and evacuated during each rotation. The number of blades and their shape, as well as the rotor’s speed, all play a role in determining how efficiently the pump operates.
Key Factors Affecting Rotor Efficiency
- Blade Shape and Number: The blades’ design can influence the volume of gas displaced with each rotation. A rotor with more blades or specially shaped blades can help improve gas handling and reduce energy consumption.
- Rotational Speed: The speed at which the rotor turns can affect the efficiency of the vacuum process. Higher speeds can increase the flow rate but may lead to higher energy consumption.
- Material Selection: The materials used to manufacture the rotor must be durable enough to withstand high rotational speeds, as well as the corrosive environments in which these pumps often operate.
The rotor’s efficient interaction with the liquid ring is essential for ensuring that the pump reaches its desired vacuum level quickly and consistently.
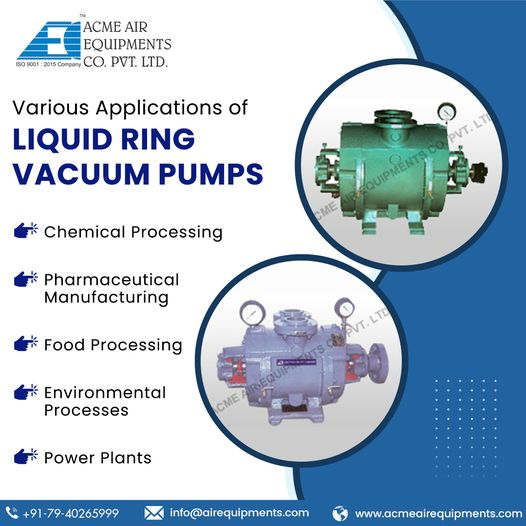
Function of the Casing in a Liquid Ring Vacuum Pump
The Role of the Casing in Pump Functionality
The casing of a liquid ring vacuum pump provides the structure and containment for the pump’s internal components. It also directs the flow of gases and liquids through the pump to ensure efficient operation. The casing plays an important role in guiding the liquid ring, maintaining the vacuum environment and preventing leaks.
The design and material of the casing are critical for maintaining the pump’s performance. It must be able to handle the pressures and temperatures generated during the vacuum process without compromising the integrity of the pump. Moreover, the casing is responsible for directing the flow of liquid to form the liquid ring, which is crucial for trapping gases and creating the vacuum.
Key Features of the Casing
- Shape and Size: The casing must be precisely engineered to ensure that the rotor can move freely within it while maintaining the liquid ring. A well-designed casing ensures optimal flow dynamics and prevents turbulence, which can reduce pump efficiency.
- Material Strength: The casing must be made from materials that can withstand high pressures and temperatures without degrading. Common materials include stainless steel and cast iron, which offer corrosion resistance and durability.
- Sealing and Leak Prevention: The casing must be properly sealed to prevent the escape of gases or liquids. Any leaks can significantly reduce pump performance and energy efficiency.
The casing’s design helps to maintain the necessary pressure differential between the inlet and outlet ports, ensuring that the pump operates at its full potential.
Seals and Shaft Assemblies Maintain the Integrity of Liquid Ring Vacuum Pumps
The Importance of Seals in Preventing Leaks
Seals play a crucial role in maintaining the integrity of liquid ring vacuum pumps. These components prevent the leakage of gases or liquids, which could otherwise compromise the vacuum level and reduce pump efficiency. Proper sealing ensures that the system remains airtight, which is essential for consistent and reliable performance.
There are several types of seals used in liquid ring pumps, including lip seals, mechanical seals and O-rings. Each type has its advantages and is selected based on the application requirements, such as temperature resistance, chemical compatibility and pressure.
Shaft Assemblies and Their Role
The shaft assembly connects the rotor to the drive motor, enabling the rotor to spin. It must be designed to handle the forces exerted by the rotating rotor, while also ensuring smooth motion and minimal friction. A properly engineered shaft assembly ensures that the rotor operates efficiently and reduces wear and tear on the internal components.
How Seals and Shaft Assemblies Impact Performance
- Seals: Effective seals prevent contamination from external elements, reduce the risk of vacuum leaks and enhance the overall reliability of the pump.
- Shaft Assemblies: A well-designed shaft assembly reduces friction and wear, which helps to minimize maintenance costs and prolong the lifespan of the pump.
Both seals and shaft assemblies are critical for ensuring that the liquid ring vacuum pump operates at peak performance and remains reliable over time.
How Liquid Ring Vacuum Pumps Work Together with Other Components?
The Interaction Between Internal Components
The interaction between the rotor, casing, seals and shaft assemblies determines the overall efficiency of the liquid ring vacuum pump. When these components work in harmony, the pump can achieve a stable and efficient vacuum with minimal energy consumption.
- Flow Optimization: The rotor works in conjunction with the casing to ensure that the liquid ring is formed correctly, which is essential for trapping and evacuating gases. The interaction between these parts ensures that the vacuum is created efficiently.
- Leak Prevention: Seals and shaft assemblies work together to prevent gas leaks, which could lead to a drop in vacuum pressure. Proper sealing ensures that the system remains airtight, which is crucial for maintaining high performance.
By optimizing the interaction between these internal components, liquid ring vacuum pumps can deliver consistent and reliable performance over long periods
FAQs about Liquid Ring Vacuum Pump
1. How does the rotor impact the efficiency of a liquid ring vacuum pump?
The rotor’s design, including its shape and number of blades, directly affects the volume of gas displaced and the overall efficiency of the pump in creating a vacuum.
2. Why is the casing design important in liquid ring vacuum pumps?
The casing provides the structure for the pump, guides the flow of liquid and gases and ensures that the liquid ring forms correctly, which is critical for vacuum efficiency.
3. How do seals prevent performance issues in liquid ring vacuum pumps?
Seals prevent leaks of gases and liquids, ensuring that the system maintains a consistent vacuum pressure and operates efficiently.
4. What role does the shaft assembly play in the operation of a liquid ring vacuum pump?
The shaft assembly connects the rotor to the drive motor and ensures smooth operation by reducing friction and wear, which contributes to the pump’s longevity and efficiency.
5. Can the interaction between these components affect the overall performance of the pump?
Yes, the proper interaction between the rotor, casing, seals and shaft assemblies is essential for ensuring that the pump operates efficiently and maintains a stable vacuum.
Conclusion
Understanding how the internal components of a liquid ring vacuum pump-such as the rotor, casing, seals and shaft assemblies-work together is key to optimizing pump performance. Each component plays a critical role in creating and maintaining the vacuum, preventing leaks and ensuring energy efficiency.
By focusing on the design and maintenance of these components, industries can maximize the efficiency and lifespan of their liquid ring vacuum pumps, reducing operational costs and downtime. For businesses relying on vacuum pumps for applications such as chemical processing, pharmaceuticals and food packaging, ensuring the optimal functioning of these internal components is essential to maintaining high productivity and efficiency.