Table of Contents
Big Bag Unloading Systems play a pivotal role in industries that handle bulk materials such as chemicals, cement, food products and more. These systems are designed to unload materials from large bags, often weighing up to 1 ton, into hoppers or other processing units. Despite their importance in ensuring smooth material handling, big bag unloading systems can face various operational challenges. From material flow issues to safety concerns, it’s essential to address these challenges for improved system efficiency and reliability.
This article explores the common challenges encountered in big bag unloading applications and provides practical solutions to enhance the system’s performance and ensure a safe, effective operation.
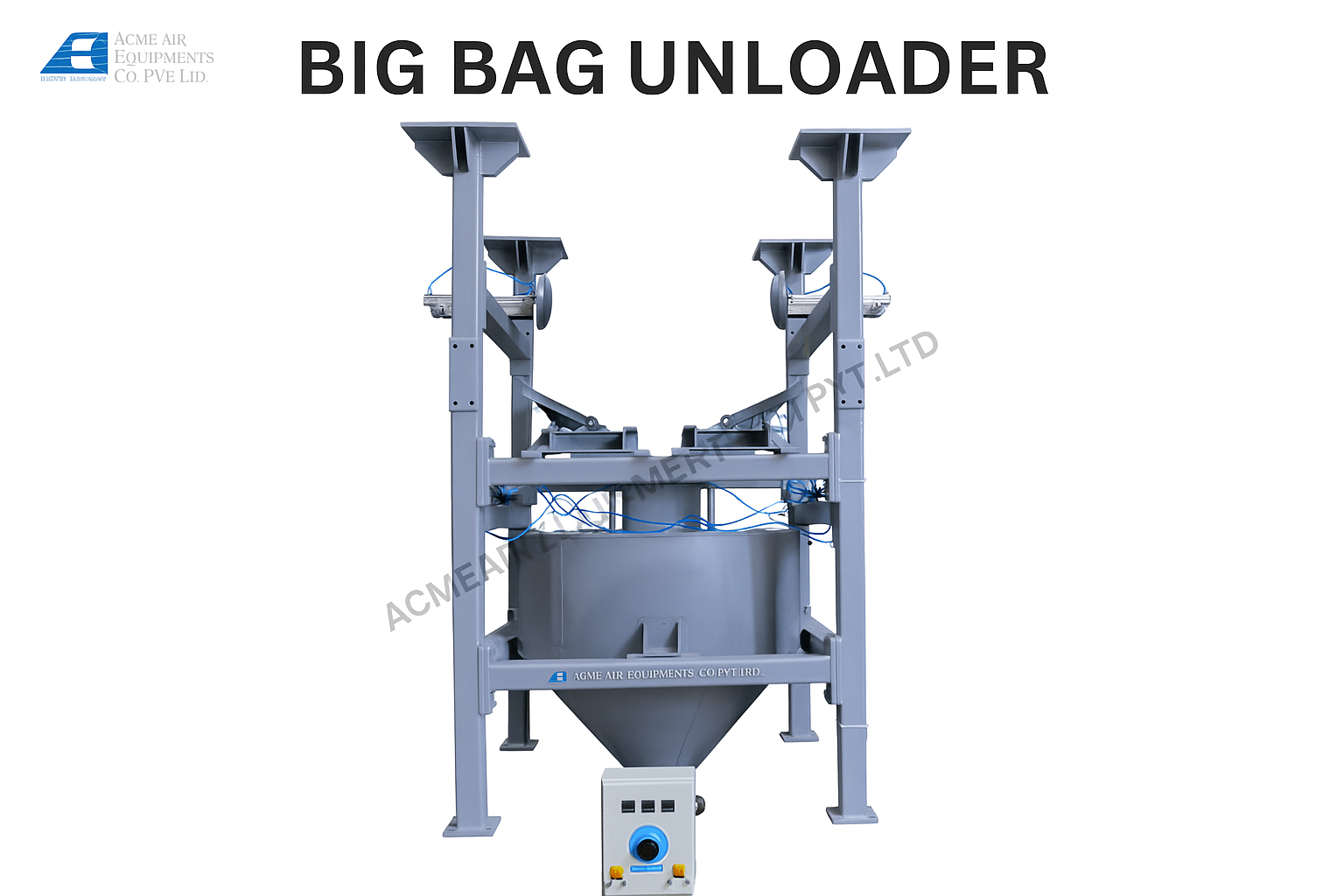
Challenges & its Solutions in Big Bag Unloading System Applications
Material Flow Blockages
Challenge:
A common problem faced in bulk bag unloading systems is the blockage of material flow. When unloading bulk bags, materials such as powders, sticky substances or materials with high moisture content may not flow smoothly into the discharge system. This results in material build-up, clogging and inconsistent discharge, which can cause production delays and system downtime.
Solution:
To address material flow blockages, consider implementing the following solutions:
- Jostling Mechanisms: Integrate vibration units or air-assisted systems that help loosen material inside the bag, encouraging smoother flow into the discharge system. The jostling mechanism agitates the bag, preventing materials from becoming compacted or clogged during unloading.
- Vibration and Agitation: Add vibration motors to the bulk unloading system. This continuous motion helps dislodge stuck materials and improves the flow into the discharge area. By ensuring materials remain loose and free-flowing, blockages can be minimized.
- Flexible Spouts and Adjustments: Use flexible discharge spouts or adjustable discharge rates to accommodate varying materials. The ability to adjust the system according to the material characteristics will help prevent clogging and improve efficiency.
- Regular Maintenance: Regularly clean and inspect components like hoppers, pipelines and discharge areas. Material accumulation in these areas can lead to blockages, so frequent maintenance is critical to keeping the system running smoothly.
Safety Concerns in Handling Heavy Bags
Challenge:
Handling heavy bags, especially those weighing up to 1 ton, can pose significant safety risks. Workers may be at risk of back injuries, muscle strains or accidents when manually handling or improperly lifting these heavy bags. These safety concerns must be addressed to ensure the well-being of personnel and prevent costly workplace injuries.
Solution:
To mitigate safety risks, ensure the following:
- Automated Lifting Systems: Use electric hoists, cranes or lifting equipment to handle big bag unloader system. These systems can lift and position the bags without manual intervention, eliminating the risk of injury associated with lifting heavy loads manually.
- Safety Features: Install safety interlocks, emergency stop buttons and load sensors to ensure that the lifting equipment operates safely. Workers should not be able to access the system while in operation.
- Ergonomics: Design the unloading system with ergonomic features, such as adjustable heights and angles, to minimize physical strain on workers. Ensuring that workers can handle materials at an optimal height reduces the risk of back or shoulder injuries.
- Training and PPE: Provide regular safety training for all personnel and ensure the use of Personal Protective Equipment (PPE), including gloves, back support and helmets, as necessary to prevent injuries.
Equipment Wear and Tear
Challenge:
Big bag unloading systems rely on several mechanical components, such as hoists, cranes and material handling systems. Over time, the constant lifting, lowering and unloading of heavy bags can result in wear and tear on these components, leading to mechanical failures and increased maintenance costs. This wear can significantly reduce the system’s efficiency and reliability.
Solution:
To prevent excessive wear and tear on the system, consider the following strategies:
- Use of Durable Materials: Ensure that key components, such as hoists, cranes and structural frames, are made from high-quality, abrasion-resistant materials. Materials like stainless steel or coated alloys are ideal for handling heavy-duty operations and preventing corrosion.
- Regular Preventive Maintenance: Implement a regular preventive maintenance schedule to inspect and replace worn-out parts before they fail. This includes lubricating moving parts, checking hoists for stress or damage and inspecting jostling mechanisms.
- Automated Monitoring: Integrate systems with a PLC (Programmable Logic Controller) to track system performance. This will help detect early signs of wear, such as abnormal vibrations or changes in load capacity, allowing for proactive maintenance.
- High-Quality Hoists and Components: Use heavy-duty hoists and material handling systems that are built to withstand repeated use. The longevity of the system will improve with quality components, reducing the frequency of repairs.
Inconsistent Material Characteristics
Challenge:
Inconsistent material characteristics, such as varying moisture content, clumping or compacting during storage, can create problems in the unloading process. These characteristics may cause materials to become difficult to discharge, leading to delays or clogging in the system.
Solution:
To address challenges caused by inconsistent material characteristics, consider these solutions:
- Adjustable Systems: Use a modular system that allows for adjustable vibration, variable hoist speeds and flow control systems. This flexibility allows the system to handle materials with varying moisture content, flowability and consistency.
- Pre-treatment Options: For materials that tend to clump or become sticky, consider pre-treatment options such as moisture control systems or drying mechanisms. These options can help stabilize the material before unloading.
- Customized Bag Design: Modify the big bag discharger to accommodate different material types by using tailored bag spouts or unloading rates. Custom designs can handle unique materials without compromising unloading efficiency.
- Vibration or Agitation Enhancements: Enhance the vibration systems to ensure materials are loosened effectively. For materials prone to clumping, a stronger or more consistent agitation system will be beneficial.
Slow Unloading Process
Challenge:
The unloading process may be slower than expected, especially when handling large volumes of material. A slow unloading process can create bottlenecks in the production line, leading to reduced overall throughput and inefficiencies in the operation.
Solution:
To address slow unloading speeds, the following upgrades can be implemented:
- Increase Hoist and Conveyor Capacity: Upgrade to high-capacity hoists and faster conveyors to handle larger volumes of material in less time. Larger hoists with increased lifting capacity will reduce the time spent unloading each bag.
- Automated Systems: Implement big bag discharger systems with programmable controls to optimize the flow rate. These systems can adapt in real-time to material characteristics and ensure faster unloading.
- Multiple Unloading Points: Consider using dual unloading points or multiple hoists to simultaneously unload more than one bag. This will reduce the time taken to unload multiple bags, improving overall throughput.
- Advanced Discharge Mechanisms: Use high-speed vibration mechanisms or air-assisted discharge systems to encourage faster material flow. This will speed up the unloading process while maintaining material quality.
Conclusion
Acme Air Equipments Co. Pvt. Ltd. provides big bag unloading systems which are essential for the efficient handling of bulk materials in many industrial operations. However, they come with several challenges, including material flow blockages, safety risks, equipment wear and inconsistent material characteristics. By understanding these common issues and implementing the right solutions, industries can improve system efficiency, reduce downtime and enhance safety.
Regular maintenance, the integration of modern technologies and designing systems that can adapt to various material types is key to overcoming these challenges. Whether you are looking to buy big bag unloading systems or optimizing your existing setup, addressing these common challenges ensures smooth and efficient operations in your facility.
FAQs about Big Bag Unloading Applications
What is a big bag unloading system?
A big bag unloading system is designed to unload bulk materials from large bags (typically up to 1 ton) into hoppers or other processing units using hoisting, vibration mechanisms and material handling systems.
What challenges are commonly faced in big bag unloading systems?
Common challenges include material flow blockages, safety risks with heavy lifting, wear and tear on equipment, inconsistent material characteristics and slow unloading speeds.
How can slow unloading speeds be addressed in big bag unloading systems?
Slow unloading speeds can be improved by using high-capacity hoists, faster conveyors, automated unloading systems and advanced discharge mechanisms.
How do I handle material flow blockages in big bag unloading systems?
Material flow blockages can be addressed by using jostling mechanisms, vibration systems, anti-clogging filters and adjustable spouts to ensure smooth material flow during unloading.