Table of Contents
Big Bag Unloading Systems, also known as big bag dischargers, are essential for industries that require the efficient and safe unloading of bulk materials stored in large bags. These systems are commonly used in industries such as chemicals, food processing, cement and pharmaceuticals. Big bag unloading systems help streamline the handling of materials like catalysts, fly ash, cement and chemicals, ensuring that they are transferred into hoppers or other containers with minimal dust and mess.
In this guide, we will walk you through the step-by-step process of installing and operating a big bag discharger system in industrial settings. This includes an overview of the necessary components, considerations during installation and the operational procedure.
Understanding the Components of a Big Bag Unloading System
Before diving into the installation process, it is important to understand the key components of a big bag unloader system. These systems are designed to handle bags typically weighing up to 1 ton, but they can be customized to handle bags of various sizes and materials. Here are the main components involved in the system:
- Rigid Frame: The sturdy structure that holds the entire system and supports the big bag during unloading.
- Jostling Mechanism: This mechanism ensures that the contents of the big bag are loosened and flow freely into the hopper or storage area. It may consist of mechanical vibration or air-blown agitation.
- Material Handling System (Electric Hoist or Crane): Used to lift and position the big bag into the unloading system. Electric hoists or cranes are commonly employed.
- Hopper/Discharge Area: The area where the material from the big bag is discharged. It typically leads to another conveyor system for further processing or storage.
- Control Panel: The control panel is used to operate the system, manage the unloading process and ensure safety.
- PLC (Programmable Logic Controller): In some cases, the system may be integrated with a PLC for automated control, reducing human intervention and improving operational efficiency.
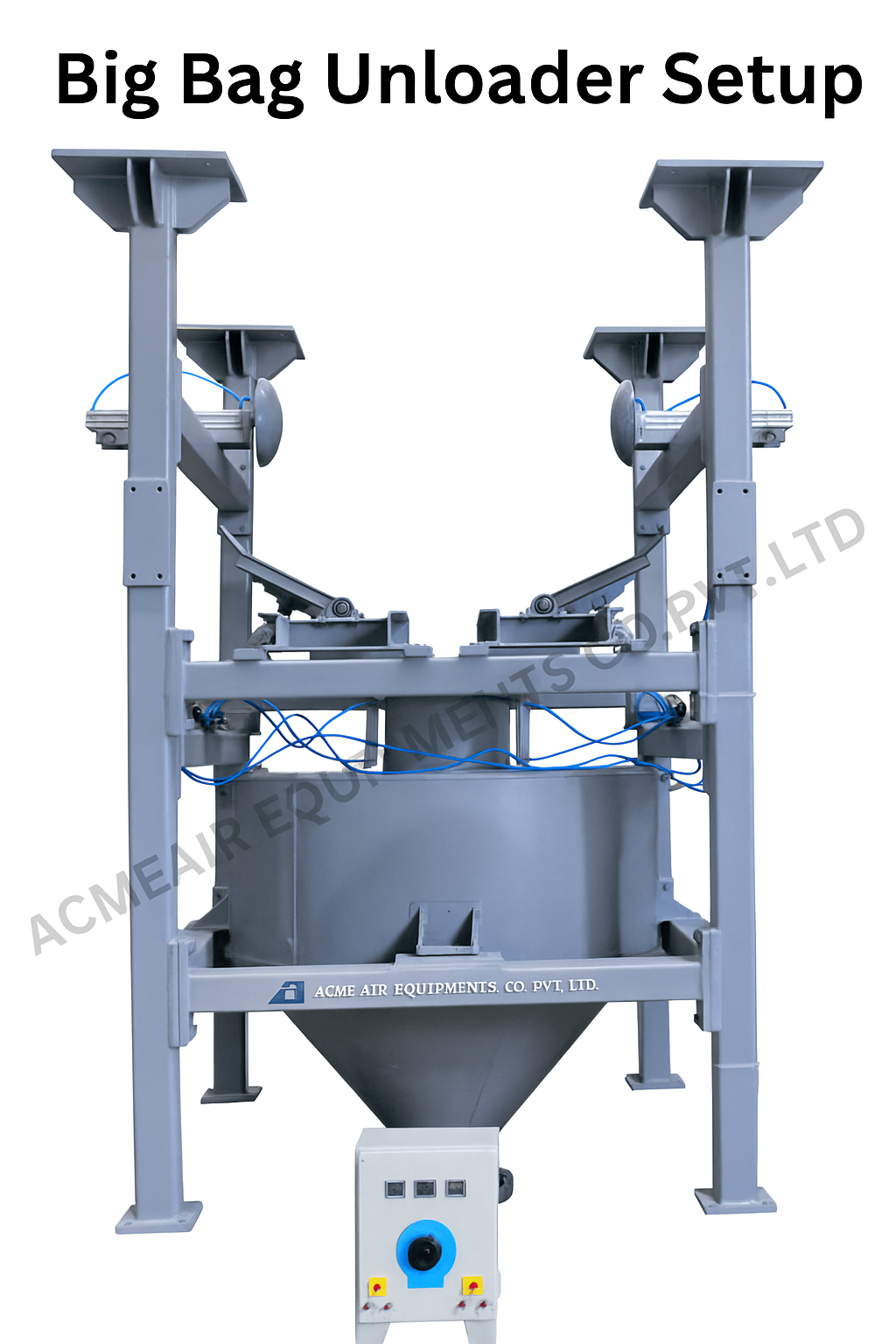
Pre-Installation Considerations
Before beginning the installation, several factors need to be taken into account to ensure smooth and safe operation of the big bag discharge system:
Site Preparation
- Space Requirements: The installation site must have sufficient space to accommodate the rigid frame, material handling equipment and storage area for big bags. Ensure there is enough clearance for hoists or cranes to operate efficiently.
- Floor Strength: The system’s frame and handling equipment can be heavy, so it’s important that the floor can support the weight of the entire system, particularly when dealing with bags up to 1 ton in weight.
- Access to Utilities: Ensure that power, air supply (if needed) and other utilities are available for the operation of the system.
- Safety Measures: Install safety features such as emergency stop buttons, safety interlocks and grounding to avoid electrical hazards during the operation.
Selecting the Right Big Bag Unloading System
- Material Type: The big bag discharger should be selected based on the type of material being unloaded. For example, if you are handling chemicals or food-grade materials, you may need a system that complies with specific standards.
- Size and Weight: Determine the size and weight capacity based on the materials to be unloaded. If your bags are larger or heavier than the typical 1-ton bags, the system may need to be customized.
Installation Steps for Big Bag Unloading Systems
Position the Rigid Frame and Material Handling Equipment
- Place the Rigid Frame: Begin by positioning the rigid frame of the bulk bag unloader system in the designated area. The frame needs to be securely anchored to the floor to prevent any movement during operation.
- Install the Hoist or Crane: Attach the electric hoist or crane to the frame, ensuring that it is positioned correctly to lift and move the big bags. Verify the lifting capacity of the hoist and ensure it matches the weight of the bags to be unloaded.
Set Up the Jostling Mechanism
- Install the Jostling Mechanism: Depending on the system, this may be a mechanical vibrator or an air-assisted system designed to shake or agitate the bag to facilitate material flow. Connect the mechanism to the control panel, if applicable.
- Test the Mechanism: After installation, conduct a test run to ensure the jostling mechanism loosens material efficiently without causing any issues with the material flow.
Configure the Hopper and Discharge Area
- Place the Hopper: Position the hopper or discharge area directly under the big bag unloading system. This is where the material will flow into once the bag is emptied.
- Connect to Conveyor Systems: If necessary, connect the hopper to downstream material handling systems like conveyors or augers to transfer the material to storage or further processing areas.
Wiring and Control Panel Setup
- Connect the Control Panel: Install and connect the control panel to manage the big bag unloading system. If the system is integrated with a PLC, ensure that the wiring is done according to the electrical specifications.
- Test Controls: After installation, test all buttons, switches and emergency stops to verify that the system is properly set up and can be controlled easily.
Operating the Big Bag Unloading System
Once the system is installed, it’s time to operate it. The following steps will guide you through the typical operation of a big bag unloading system:
Prepare the Bag for Unloading
- Place the Big Bag: Using the hoist or crane, position the big bag onto the unloading station. Ensure the bag is secured and the spout is positioned correctly to avoid spillage.
- Check for Material Compatibility: Ensure that the material in the bag is compatible with the system’s capabilities and that the material handling equipment is appropriately set up.
Activate the System
- Start the System :Using the control panel, activate the system and begin the unloading process. The hoist will lift the big bag and the jostling mechanism will begin to agitate the bag, allowing the material to flow into the hopper.
Unload the Material
- Monitor the Flow: Observe the material as it flows from the bag into the hopper or discharge area. If needed, adjust the flow rate or jostling mechanism to improve unloading efficiency.
- Check for Blockages: If any blockages occur during the unloading process, stop the system and clear the obstruction. Regularly inspect the equipment for wear and tear, especially the material handling components.
Finish the Unloading Process
- Lower the Bag: Once the material has been fully unloaded, lower the empty big bag using the hoist or crane.
- Seal the System: Ensure the unloading system is cleaned and sealed properly to prevent contamination or dust exposure.
Regular Maintenance and Safety Checks
To ensure optimal performance, big bag unloading systems require regular maintenance and safety checks. Follow these guidelines:
- Check for Wear and Tear: Regularly inspect components such as hoists, jostling mechanisms and filters for wear and tear.
- Clean the System: Clean the replace filters as needed to maintain air quality and system efficiency.
- Safety Checks: Test the emergency stop functions, control panel and other safety features to ensure they are operational.
Conclusion
Acme Air Equipments Co. Pvt. Ltd., as a leading manufacturer of big bag unloading system in an industrial setting involves careful planning, the proper installation of key components and thorough operation procedures. By following the steps outlined in this guide, industries can ensure that its unloading systems function smoothly, improving efficiency and reducing the risks associated with material handling.
Regular maintenance and adherence to safety protocols are essential to keeping the system running at peak performance. Whether you are looking to buy big bag unloading systems for your facility or are already operating one, understanding the setup and operation process will help you optimize the performance of your equipment.
FAQs about Big Bag Unloading Systems
What is a big bag unloading system?
A big bag unloading system is industrial equipment designed to efficiently unload bulk materials from large bags (typically weighing 1 ton) into storage containers or processing systems, using hoists, jostling mechanisms and material handling systems.
How does a bulk bag unloading system work?
A bulk bag unloading system lifts the big bag using a hoist, while the jostling mechanism loosens the material inside, allowing it to flow freely into the discharge area or hopper. Dust collection systems are also integrated to minimize airborne particles.
Can a big bag unloading system handle different types of materials?
Yes, a big bag discharger can be customized to handle a wide range of materials, including chemicals, powders, cement and food-grade materials, based on the specific needs of the industry.
What are the benefits of using a big bag unloading system?
Benefits include increased efficiency, reduced manual labor, enhanced safety, reduced dust exposure and compliance with environmental regulations.