Table of Contents
In industrial applications, the efficiency of a vacuum system plays a critical role in ensuring smooth operations, productivity and cost-effectiveness. Mechanical Vacuum Boosters have gained popularity due to their superior performance, versatility and energy efficiency. These systems are designed to handle a variety of applications, from distillation and degassing to refining and semiconductor processing.
In this article, we will explore the top benefits of using vacuum boosters in industrial processes, highlighting how these systems improve operational efficiency and reduce overall costs.
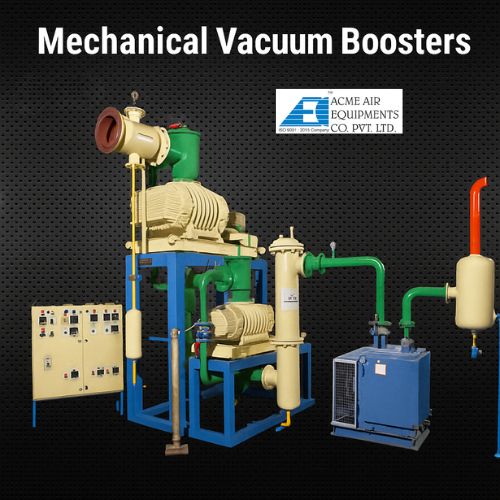
Enhanced Performance and Efficiency
One of the key benefits of using a mechanical vacuum booster is the enhanced performance it offers compared to traditional vacuum pumps. These systems are designed to provide a high flow rate, which is crucial in processes that require high vacuum levels. Mechanical vacuum boosters work by augmenting the vacuum pressure generated by the primary vacuum pumps, leading to faster and more efficient operations.
In addition, roots vacuum boosters operate with minimal friction between the moving components, which results in a smoother and more reliable performance. The design ensures that the mechanical vacuum booster maintains stable suction and pressure levels throughout its operation, contributing to higher efficiency and reduced downtime.
For industries that rely on continuous, high-demand processes such as vacuum distillation and vacuum freeze drying, having a high-speed vacuum booster ensures optimal efficiency with minimal interruptions.
Energy Cost Reduction
Energy consumption is a significant concern in most industrial operations. Since vacuum booster systems work in tandem, they are able to provide the necessary vacuum levels while consuming less power compared to traditional systems. This is especially important in industries that operate at a large scale, where even small improvements in energy efficiency can lead to substantial savings.
Mechanical vacuum boosters are designed to optimize the energy used during vacuum generation. By providing precise and constant volume displacement at rated conditions, these systems reduce unnecessary energy consumption. The ability to handle gases and vapors at lower specific power consumption ensures that roots vacuum boosters are a more energy-efficient alternative, helping businesses lower their operational costs and improve their bottom line.
Increased Process Reliability
Mechanical vacuum boosters are known for their reliability in various industrial applications. Whether it’s for vacuum impregnation, degassing or coating, these systems provide consistent and stable vacuum levels, contributing to the overall stability of the process. Their design, which often includes twin or tri-lobe rotors, minimizes wear and tear, resulting in longer service life and less frequent maintenance.
By maintaining a consistent vacuum level, mechanical vacuum boosters help prevent process disruptions that can occur due to fluctuating pressure. This ensures that the desired process conditions, such as temperature, pressure and flow rates, are maintained, leading to more predictable and reliable outcomes in operations like semi-conductor processing and vacuum freeze drying.
Versatility in Industrial Applications
Another notable benefit of mechanical vacuum boosters is their versatility. These systems are capable of handling a wide range of industrial applications, from oil refining and distillation to vacuum coating and space simulation. The flexibility of mechanical vacuum booster systems makes them suitable for industries with diverse needs, such as pharmaceuticals, food processing and semiconductor manufacturing.
For example, in vacuum distillation, mechanical vacuum boosters provide the necessary vacuum pressure to separate components based on their boiling points, making them ideal for the refining of industrial oils. Similarly, in vacuum impregnation, these systems help achieve uniform material saturation in a variety of substrates, such as metals and plastics.
Furthermore, mechanical vacuum boosters can be customized to meet the specific requirements of different industries, making them an essential tool for any industrial process that relies on precise vacuum control.
Low Maintenance and Longer Service Life
The design and construction of mechanical vacuum boosters are engineered to be low-maintenance and durable. These systems are designed with components that experience minimal friction and wear, extending the service life of the equipment. The lack of physical contact between rotating components in the system helps prevent excessive wear, ensuring that the equipment continues to perform optimally for an extended period.
Additionally, the advanced engineering reduces the likelihood of malfunctions, decreasing the need for frequent repairs. This results in reduced downtime and maintenance costs, which ultimately contributes to the overall efficiency of the industrial process.
Compact and Space-Efficient Design
Many industrial operations require equipment that doesn’t take up too much space while still delivering high performance. Vacuum booster systems are designed with making them ideal for applications where space is limited. Their compact design ensures that they can be easily integrated into existing systems without requiring significant modifications to the plant layout.
In industries such as space simulation and semi-conductor processing, where space is often at a premium, the space-efficient nature of mechanical vacuum boosters makes them a suitable choice. Their modular design also makes them easy to install and maintain in a variety of settings.
Conclusion
Acme Air Equipments Co. Pvt. Ltd., provides mechanical vacuum boosters in industrial processes offers a wide range of benefits, including enhanced performance, energy cost reduction, increased reliability and versatility. These systems are designed to improve the efficiency and stability of processes that rely on precise vacuum control, from oil refining and vacuum impregnation to vacuum distillation and semiconductor manufacturing. With their low-maintenance design, longer service life and compact structure, mechanical vacuum boosters are an essential part of modern industrial operations.
As industries continue to prioritize energy efficiency and process optimization, the use of mechanical vacuum booster systems will undoubtedly play a critical role in driving these goals forward. Whether you are looking to improve the efficiency of your current vacuum system or seeking a reliable solution for new industrial applications, mechanical vacuum boosters offer the performance and reliability that modern industries require.
FAQs about Mechanical Vacuum Boosters
What is a mechanical vacuum booster?
A mechanical vacuum booster is a device that enhances the performance of a vacuum system by augmenting the vacuum pressure produced by the primary vacuum pump, enabling faster and more efficient operations in industrial applications.
How does a mechanical vacuum booster reduce energy costs?
Mechanical vacuum boosters are designed to operate with lower specific power consumption, providing precise and constant volume displacement, which helps reduce overall energy consumption compared to traditional vacuum systems.
What are some common applications of mechanical vacuum boosters?
Mechanical vacuum boosters are used in various applications, including vacuum distillation, vacuum impregnation, degassing, oil refining and semiconductor processing.
How do mechanical vacuum boosters improve process reliability?
These systems maintain consistent vacuum levels, reducing fluctuations in pressure that could disrupt industrial processes, thus ensuring stable and reliable operations.
What makes mechanical vacuum boosters low-maintenance?
The design of mechanical vacuum boosters minimizes friction and wear between moving parts, reducing the need for frequent maintenance and extending the equipment's service life.