Table of Contents
Pneumatic conveying systems are integral to material handling in industries such as food processing, pharmaceuticals, chemicals and cement production. These systems use air or gas pressure to transport bulk materials efficiently, offering a flexible and reliable solution for conveying powders, granules and pellets. However, like any complex system, pneumatic conveyors can face issues that hinder performance and productivity. Understanding these common issues and knowing how to troubleshoot them is essential for maintaining the efficiency and reliability of pneumatic conveying equipment.
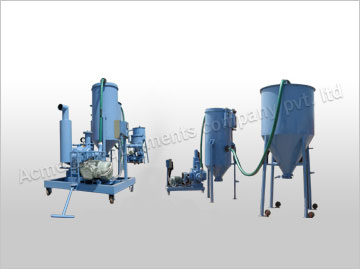
This article will explore some of the most common issues faced in pneumatic conveying systems and provide troubleshooting tips to address these challenges effectively.
Material Blockages and Clogging
Issue:
One of the most common problems in pneumatic material conveying systems is material blockages or clogging in the pipelines. This can occur when the material being conveyed is not flowing as expected, often due to factors like high moisture content, particle size inconsistency or insufficient air velocity. Blockages can lead to a drop in system efficiency and, in some cases, system shutdowns.
Troubleshooting Tips:
- Increase Airflow: Check the pneumatic conveying system’s air supply and ensure that the airflow is sufficient to keep the material moving. If air velocity is too low, consider adjusting the settings of the blower or compressor.
- Adjust Pressure: In systems with varying material types, ensure the correct pressure is maintained. Dense phase pneumatic conveying systems typically require higher pressures for conveying denser materials, while dilute phase pneumatic conveying works well for lighter, bulk materials.
- Check for Pipe Obstructions: Regularly inspect the piping for debris or build-ups. Cleaning the pipes periodically can help avoid material blockages. Consider implementing inline cleaning devices to ensure consistent material flow.
- Use Vibrators or Agitators: Install vibrators or agitators in the discharge or hopper area to help keep materials moving and prevent them from clumping or sticking to the sides.
Inconsistent Material Flow
Issue:
Inconsistent material flow can occur in pneumatic transfer systems when there is a fluctuation in the material volume or when the materials being conveyed have inconsistent properties. This issue may manifest as uneven material transport, where some parts of the system receive more material than others, leading to operational inefficiencies.
Troubleshooting Tips:
- Ensure Proper Material Segregation: For materials with different densities, ensure that the system is set up to handle each type accordingly.
- Check for Pressure Variations: Pressure fluctuations in the system can result in inconsistent flow. Check for air leaks or faulty regulators that could be causing inconsistent pressure. Fixing these will help maintain steady material flow.
- Monitor Material Feed Rates: Ensure that the feeding mechanism is functioning correctly and feeding a consistent amount of material into the system. If the feed rate is inconsistent, it will directly impact material flow.
- Upgrade to High-Flow Pneumatic Conveyors: If material flow is still inconsistent despite troubleshooting, consider upgrading to a high-flow pneumatic conveyor system that is better suited to handle a larger volume or variety of materials.
Wear and Tear of Components
Issue:
Over time, the components of a pneumatic conveying system are subjected to wear and tear, especially when handling abrasive materials. This can lead to increased friction, which causes damage to internal parts like pipes, filters and valves. Such wear and tear can reduce system efficiency and may lead to unplanned maintenance and downtime.
Troubleshooting Tips:
- Upgrade to Durable Materials: For systems handling abrasive materials, ensure that parts such as pipes and elbows are made from wear-resistant materials like stainless steel or ceramic-lined components.
- Regular Inspection: Schedule regular maintenance and inspection intervals to detect any signs of wear before it leads to system failure. Focus on areas like pipe joints, filters and airlocks, which are prone to abrasion.
- Lubrication and Coatings: For moving components, ensure proper lubrication. In areas with heavy wear, apply protective coatings to reduce friction and prevent premature wear.
- Replace Worn Components: As part of regular maintenance, replace worn-out components promptly. This includes valves, filters and rotary airlocks, all of which can be impacted by regular use.
Pressure Loss or Air Leaks
Issue:
Pressure loss or air leaks in pneumatic conveyor systems can significantly affect system performance. If the system is not able to maintain the required air pressure, the material flow can become erratic or the conveying process may stop entirely.
Troubleshooting Tips:
- Inspect for Leaks: Inspect the entire pipeline for leaks, especially around junctions, valves and flanges. Use soapy water to detect leaks or employ leak detection equipment for a more thorough inspection.
- Monitor Air Pressure: Regularly monitor the system’s air pressure and compare it with the manufacturer’s specifications. If the pressure is too low or too high, adjust it accordingly.
- Replace Worn Seals: Over time, seals in the system may wear out and cause leaks. Regularly check and replace worn seals to prevent air loss.
High Energy Consumption
Issue:
High energy consumption is a common issue in pneumatic conveying systems, particularly in systems that operate at high pressures or with larger materials. This inefficiency can lead to higher operational costs and reduced profitability.
Troubleshooting Tips:
- Install Variable Speed Drives (VSDs): Variable speed drives can help regulate the speed of the blower or compressor, providing just the amount of air pressure needed for the system and reducing energy use.
- Use Efficient Equipment: Consider upgrading to more energy-efficient equipment, such as energy-saving pneumatic conveyor systems, which can help reduce overall energy consumption.
- Regular Maintenance: Ensure that the system is regularly serviced to keep it running efficiently. Dirty filters, worn components and other issues can cause the system to work harder, increasing energy consumption.
Overheating of Pneumatic Equipment
Issue:
Overheating is another issue that can arise in pneumatic systems, particularly when the equipment is running continuously under heavy loads. Overheating can damage components, leading to breakdowns and reduced system longevity.
Troubleshooting Tips:
- Check Airflow: Ensure that the blower or compressor is properly ventilated and that air intake filters are clean. Restricted airflow can lead to overheating of equipment.
- Monitor Operating Conditions: Keep track of operating temperatures and airflow rates. If temperatures rise too high, consider adding additional cooling or ventilation systems to regulate the temperature.
- Use Properly Sized Equipment: Ensure that the equipment, including the blower, compressor and pipes, is properly sized for the material handling requirements. Overloading equipment can cause it to overheat and fail prematurely.
- Regular Maintenance: Regularly clean and inspect components to ensure they are not operating under strain. Maintenance of cooling systems is also crucial to preventing overheating.
Conclusion
Acme Air Equipments Co. Pvt. Ltd. offers Pneumatic conveying systems which are essential for the efficient and reliable transportation of bulk materials in various industries. However, common issues such as material blockages, safety concerns, equipment wear and air leaks can impact system performance. By understanding these challenges and implementing the appropriate troubleshooting tips, industries can ensure that their pneumatic conveying equipment operates smoothly and efficiently.
Regular maintenance, proper equipment sizing and optimization of airflow and pressure are crucial to preventing downtime, reducing operational costs and enhancing system reliability. Whether you are managing a pneumatic vacuum conveying system, addressing these issues proactively will improve your system’s efficiency and longevity.
FAQs about Pneumatic Conveying Systems
What are the common issues faced in pneumatic conveying systems?
Common issues include material flow blockages, air leaks, equipment wear and tear, inconsistent material flow, slow unloading speeds and high energy consumption.
How can material flow blockages in pneumatic systems be prevented?
Material flow blockages can be prevented by using vibrators, air-assisted systems and adjustable spouts. Regular maintenance and cleaning of the system also help reduce blockages.
How can energy consumption in pneumatic conveying systems be reduced?
Energy consumption can be reduced by optimizing airflow, installing variable speed drives and maintaining efficient equipment.
What should I do if I notice air leaks in my pneumatic system?
If air leaks are noticed, inspect the entire pipeline, including junctions, valves and flanges. Replace worn seals and check the compressor to ensure optimal performance.