Table of Contents
The chemical and fertilizer industries face continuous pressure to optimize their bulk material handling processes while dealing with complex materials that are often abrasive, dusty or moisture-sensitive. From raw ingredient intake to post-processing transfer, ensuring clean, efficient and safe movement of solids like urea, phosphates, nitrates, potash and chemical powders is essential to maintain product quality, process continuity and workplace safety.
Traditional mechanical systems, such as screw or belt conveyors, frequently struggle to meet the demands of modern fertilizer and chemical plants, especially under high-volume, high-speed conditions. In this context, pneumatic conveyor systems are increasingly being adopted as a strategic solution to address the most pressing challenges in bulk material transport.
This article examines how pneumatic conveying systems are being implemented across chemical and fertilizer operations and why they are critical for improving handling performance, minimizing product degradation and meeting rising operational and regulatory expectations.
Bulk Material Handling: The Specific Challenges in Fertilizer and Chemical Manufacturing
Nature of Materials Handled
In both fertilizer and chemical plants, the materials handled have complex physical properties:
- Abrasive: Minerals like potash and ammonium sulfate can wear out components quickly.
- Dusty: Powdered additives and raw chemicals often create airborne particles, leading to safety risks.
- Hygroscopic: Materials such as urea tend to absorb moisture and cake, leading to flow blockages.
- Toxic or Hazardous: In chemical manufacturing, material containment is critical to avoid exposure and contamination.
These properties demand a conveying method that can transport materials gently, cleanly and efficiently-requirements that pneumatic material conveying systems are designed to meet.
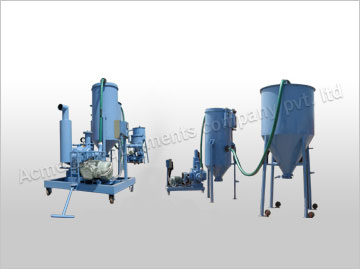
High Throughput, 24/7 Demands
Large-scale fertilizer plants run continuously, feeding mixers, blenders, granulators, dryers and packaging systems in tandem. Material must move uninterrupted and with precision, making downtime extremely costly.
Pneumatic transport systems can move bulk materials quickly and reliably, with reduced mechanical failures and less operator intervention compared to mechanical conveyors
How Pneumatic Conveyor Systems Solve Bulk Material Handling Issues?
Enclosed Transfer and Dust Suppression
Dust is one of the major operational and safety challenges in fertilizer and chemical manufacturing. Fugitive emissions not only pose health hazards but also increase the risk of explosions. Pneumatic conveying provides enclosed systems that eliminate dust at the source, protecting both personnel and the environment.
In ammonium nitrate or phosphate-based fertilizer production, pneumatic vacuum conveying systems prevent the escape of fine particles during transfer-critical in both blending and drying stages.
Wear Resistance and Long-Term Durability
In abrasive environments-like those handling potash or chemical catalysts-mechanical components often suffer rapid wear. In contrast, pneumatic conveyors, especially dense phase systems, move materials at low velocity, significantly reducing internal pipeline erosion and extending system life.
Using wear-resistant bends, ceramic-lined pipes and tailored airflow designs, manufacturers can handle even the most abrasive materials without frequent downtime or component replacement.
Minimal Residue and Product Cross-Contamination
Cross-contamination is a serious issue when switching between different fertilizer blends or chemical products. Traditional conveyors require thorough cleaning between batches. In pneumatic transfer systems, the enclosed airflow ensures minimal product hang-up and can be quickly purged between runs-making them ideal for batch processes or multi-product lines
Application of Pneumatic Conveying in Fertilizer Production Lines
Raw Material Intake and Transfer
Fertilizer production often begins with bulk unloading of raw materials such as rock phosphate, potash, sulfur and urea. These materials are transferred from silos or receiving hoppers into mixing and compounding areas. Pneumatic conveyor systems ensure continuous transfer from bulk silos to production points without manual handling or external contamination.
Blending and Granulation Support
During blending and granulation, precise feeding of additives, binders and base materials is required. Pneumatic systems offer flow control and automation that support consistent feed rates-critical in forming uniform granules. In granulation lines, pneumatic conveying also serves as a vital link to drying and cooling units.
Finished Product Conveying to Storage or Packaging
After granules are coated and dried, they must be transferred to storage bins or packaging lines. Pneumatic conveying systems help maintain granule integrity while ensuring clean transfer. This is especially important in specialty fertilizer manufacturing, where consistency affects product performance.
Solving Chemical Plant Challenges with Pneumatic Transport Systems
Handling Reactive or Hazardous Materials
Many chemicals, such as aluminum chlorohydrate or polymer additives, must be conveyed in systems that prevent human contact and environmental exposure. Pneumatic conveying systems, with sealed pipelines and automated controls, provide an ideal solution for these sensitive materials.
In batch chemical plants, where frequent recipe changes occur, pneumatic systems can be flushed or air-purged, minimizing downtime between product switches.
Moisture Control and Flowability
Moisture-sensitive materials can cake or clump in mechanical conveyors, causing blockages. With pneumatic conveying, dry air or nitrogen can be used as the conveying medium to keep materials fluid and free-flowing, which is especially beneficial for chemical powders that degrade in humid conditions.
Integrating Pneumatic Conveyors for Operational Excellence
System Design Customization
A pneumatic conveyor manufacturer designs system based on the chemical nature, particle size and flow behavior of the material. Whether it’s for vacuum, pressure or hybrid configurations, system design must consider:
- Pipeline routing (vertical and horizontal)
- Airflow control
- Abrasion resistance
- Automation and sensor integration
A customized pneumatic conveying system ensures optimal performance without over-engineering or unnecessary energy costs.
Automation and Digital Monitoring
Modern fertilizer and chemical facilities integrate pneumatic conveying systems with PLCs and smart monitoring tools. Real-time data on flow rate, pressure and temperature ensures precise delivery and allows predictive maintenance. Operators can control the entire conveying process remotely, improving uptime and reducing labor costs.
FAQs about Pneumatic Conveying Systems
1. Why are pneumatic conveying systems ideal for fertilizer manufacturing?
They handle abrasive and dusty materials in enclosed systems, reducing product loss and improving worker safety.
2. Can pneumatic conveyors manage reactive or hazardous chemicals?
Yes, they offer sealed, automated transport that minimizes exposure and contamination, critical for chemical plant safety.
3. What’s the benefit of dense phase pneumatic conveying in bulk handling?
It allows low-velocity transfer of fragile or abrasive materials, minimizing wear and degradation.
4. How does pneumatic conveying reduce contamination risks?
Enclosed pipelines prevent cross-contamination and dust emission, essential for product quality and compliance.
Conclusion
Efficient bulk material handling is foundational to the success of the chemical and fertilizer industries. The complexity and variability of materials handled in these sectors make conventional mechanical conveyors insufficient for meeting modern operational demands.
Pneumatic conveying systems offer a reliable, flexible and contamination-free solution to these challenges. Whether dealing with abrasive mineral fertilizers or sensitive chemical powders, these systems provide the performance, safety and automation required in today’s high-throughput, quality-driven manufacturing environments.
As the demand for safe and efficient bulk handling continues to rise, the adoption of pneumatic material conveying systems will become not only a competitive advantage but a necessity in the fertilizer and chemical sectors.