Table of Contents
Turbo blowers are high-performance, high-speed devices designed to move air at high pressures efficiently. As industries across the globe strive for energy savings and operational excellence, the popularity of turbo blowers has surged due to their exceptional efficiency and performance. In this article, we’ll explain in depth the working principle of turbo blowers and how they contribute to higher efficiency in various industrial applications.
Understanding the Working Principle of Turbo Blowers
The working principle of a turbo blower is based on its ability to generate compressed air using high-speed rotating turbines or rotors. Unlike traditional mechanical blowers that rely on gears and oil for lubrication, high-speed turbo blowers operate without such components, making them simpler, more efficient and easier to maintain. Let’s break down the working mechanism step by step.
High-Speed Rotor and Turbine Dynam ics
The heart of a Turbo Blowers is its high-speed rotor or turbine. This rotor is typically powered by an electric motor or a variable frequency drive (VFD), allowing it to rotate at very high speeds – often exceeding revolutions per minute (RPM). This high speed is the key to the turbo blower’s ability to compress air efficiently.
When the rotor spins, it creates a powerful centrifugal force that draws in air at the inlet. As the air is pulled into the system, it is rapidly accelerated due to the fast rotation of the turbine blades or rotor blades. This high-speed action causes the air molecules to increase their velocity, preparing them for compression.
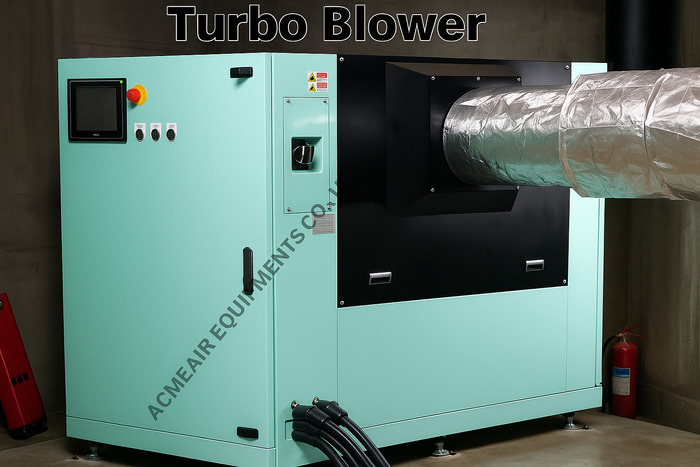
Centrifugal Compression Process
Once the air is drawn in, the high-speed rotor directs it towards the edges of the compressor where the centrifugal force compresses it. The term turbo refers to the high-speed spinning turbine or rotor, which is responsible for driving the centrifugal compression process.
In centrifugal blowers like the turbo blower, the compressed air is generated by pushing the incoming air outward along the blades of the rotor, typically in a circular or spiral direction. The centrifugal force that results from the rotor’s high speed increases the air pressure as it moves through the blower’s housing.
The Role of the Diffuser and Air Bearings
As the high-speed air exits the rotor, it enters a diffuser, which is a carefully designed chamber that slows down the fast-moving air. The diffuser allows the high-velocity air to expand and convert some of its kinetic energy into pressure, resulting in further compression of the air. This is a key part of the blower’s efficiency, as it reduces the overall load on the rotor and helps in producing high-pressure air.
Another critical part of the mechanical design of centrifugal turbo blowers is the air-bearing system. In traditional blowers, mechanical bearings or oil-lubricated systems are used to support the rotating shaft. However, in turbo blowers, air-bearings (or in some cases, magnetic bearings) are used to support the high-speed rotor. These bearings are crucial in minimizing friction, which results in less wear and tear on components and significantly reduces the need for oil or lubrication, improving efficiency and reducing maintenance.
Air-bearing technology ensures that the rotor floats with minimal friction, allowing it to achieve extremely high speeds and ensuring the blowers can handle the required operational pressures without the need for oil, which also reduces the environmental impact and operational costs.
Pressure and Flow Regulation
As the air moves through the system, it is compressed further as it exits through the discharge port. The high-speed rotor has the capability to generate very high flow rates, which makes turbo blowers ideal for applications that require consistent, high-pressure air over extended periods. The compressed air exits the blower with higher pressure than at the inlet, thus increasing the overall system pressure.
The pressure ratio is regulated through the high-speed rotor, which adjusts its rotational speed based on the required air pressure. Many turbo blowers come equipped with a Variable Frequency Drive (VFD) that allows for real-time adjustments to the rotor speed, ensuring that the system operates efficiently even when demand fluctuates. This means that turbo blower can adapt to variable loads, making them more efficient than traditional blowers, which often operate at a fixed speed.
No Gears or Belts – Direct Drive Design
One of the key features that set turbo air blowers apart from other types of blowers is the direct-drive design. Instead of using mechanical gear systems or belts to transmit power to the blower’s rotor, high-speed turbo blowers are powered directly by an electric motor. This design eliminates the need for additional components like gears or v-belts, which can often add complexity, wear and maintenance to the system.
The direct-drive mechanism improves efficiency by reducing power losses that can occur through the friction in traditional gear-driven systems. This streamlined setup contributes to a more compact, lighter and energy-efficient blower, which makes it ideal for use in various industrial processes, from water treatment to pneumatic conveying.
Efficiency of Turbo Blowers
The efficiency of turbo blowers is what makes them particularly attractive in industries where energy consumption is a major concern. The high efficiency of these blowers comes from their streamlined design, advanced materials and high-speed rotor systems. Let’s look at how turbo blowers achieve such high performance.
Energy Efficiency
One of the main reasons high-performance turbo blowers are so efficient is their ability to produce significant amounts of compressed air without consuming excessive energy. This is because they operate without oil, gears or belts, reducing friction and mechanical losses. The air-bearing or magnetic bearing technology allows for minimal wear on moving parts, enabling the blower to operate at peak efficiency for longer periods.
With high-speed turbo blowers, the ability to adjust the rotor speed based on demand (via Variable Frequency Drive) allows the blower to only consume as much power as needed, further optimizing energy use. This makes turbo blowers a highly flexible solution for industries that experience fluctuations in their air requirements, such as wastewater treatment plants and chemical processing facilities.
Low Maintenance Requirements
Since turbo blowers are oil-free, require no gears or belts and use air-bearings for rotor support, the maintenance requirements for these systems are minimal compared to traditional blowers.
The absence of oil lubricants means there is no need to regularly change oil or worry about oil contamination in the air system. This not only reduces the operational costs but also minimizes downtime for maintenance, increasing productivity.
Moreover, turbo blowers have fewer moving parts than traditional blowers, which translate to fewer opportunities for parts to wear out. As a result, turbo blowers have a much longer lifespan and are less prone to breakdowns, offering better reliability and less frequent need for repairs.
High-Performance in Demanding Applications
The efficiency of industrial turbo blowers also comes from their ability to perform in demanding applications, where high air pressure and large airflows are required. These blowers can provide continuous high-pressure air for extended periods, making them suitable for aeration, filter backwashing, membrane applications and other demanding industrial processes. The compact turbo blowers provide high flow rates without occupying large amounts of space, further adding to their versatility.
Turbo blowers are also capable of handling variable loads, allowing them to adjust output based on the required air pressure. This adaptability improves overall system efficiency by reducing energy consumption when demand is lower.
Conclusion
The working principle of turbo blowers is a combination of advanced technology and efficient design. At their core, turbo blowers utilize high-speed rotors and centrifugal force to generate high-pressure compressed air. The integration of air-bearing technology and the direct-drive design eliminates the need for traditional oil lubrication, gears and belts, reducing friction and improving efficiency.
Acme Air Equipments Co. Pvt. Ltd., offers Turbo blowers which are highly efficient, offering exceptional energy savings, reduced maintenance and long-term reliability. Their ability to provide high flow rates with minimal power consumption, along with their compact design, makes them ideal for applications such as wastewater treatment, chemical processing and pneumatic conveying. By understanding the working principle and efficiency of high-speed turbo blowers, industries can make informed decisions on their integration into various processes, driving both operational efficiency and cost savings.
FAQs about Turbo Blowers
How do turbo blowers work?
Turbo blowers work by using a high-speed rotor or turbine to compress air through centrifugal force. The air is drawn in and accelerated by the rotor, then compressed in a diffuser before being discharged at high pressure.
What makes turbo blowers more efficient than traditional blowers?
Turbo blowers are more efficient because they operate without gears or belts, use air-bearings for minimal friction and have the ability to adjust speed based on demand, optimizing energy consumption.
What is the role of the high-speed rotor in a turbo blower?
The high-speed rotor in a turbo blower generates centrifugal force, which accelerates and compresses air, allowing the blower to produce high-pressure air efficiently without the need for mechanical components like gears.
How does the air-bearing system improve turbo blower performance?
The air-bearing system supports the rotor without friction, allowing it to operate at high speeds with minimal wear, reducing the need for lubrication and increasing efficiency and longevity.
What are some common applications of turbo blowers?
Turbo blowers are commonly used in wastewater treatment, chemical processing, pneumatic conveying and aeration systems, where high-efficiency compressed air is required.