Table of Contents
In industries where solvents are integral to production-such as pharmaceuticals, chemicals and coatings-the ability to recover and reuse these solvents is both an economic and environmental necessity. Solvent recovery systems are designed to separate and reclaim solvents from process gases, allowing manufacturers to reduce waste, minimize emissions and lower operating costs. A critical component in achieving these goals is the Two Stage Liquid Ring Vacuum Pump.
These specialized pumps are engineered to handle high vapor loads while maintaining low vacuum pressures, making them ideal for solvent recovery applications. Unlike standard vacuum pumps, the two-stage design allows for greater efficiency in condensing and capturing solvent vapors, even under demanding process conditions. This article explores how two stage vacuum pumps are used in solvent recovery operations and why their performance characteristics make them essential in modern process industries.
The Purpose of Vacuum Pumps in Solvent Recovery Systems
Solvent recovery involves capturing solvent vapors from process streams-typically in evaporation, distillation or drying operations-and condensing them back into reusable liquid form. This process often requires a vacuum environment to lower boiling points and promote vaporization at reduced temperatures.
Two stage vacuum pumps are specifically suited for this task because they can sustain low absolute pressures, which are critical for vaporizing solvents with low boiling points. By maintaining a deeper and more stable vacuum, they improve vapor extraction and make condensation more efficient downstream. This ensures that solvent recovery units can operate continuously and effectively, without vapor bypass or inefficient recovery cycles.
Why Two Stage Liquid Ring Vacuum Pumps Are Suited for Solvent Recovery?
Deep Vacuum for Efficient Vaporization
The defining advantage of two stage liquid ring vacuum pumps is their ability to achieve deeper vacuum levels than single-stage designs. This capability is vital in solvent recovery systems where the goal is to recover solvents like acetone, ethanol, methanol and isopropanol-compounds that evaporate easily under vacuum but require stable low pressure to condense effectively.
By compressing vapor in two sequential stages, these pumps reduce vapor pressure incrementally, preventing shock loads and ensuring smoother flow through the recovery system. This allows solvent vapor to be drawn more completely from process equipment and condensed with higher efficiency.
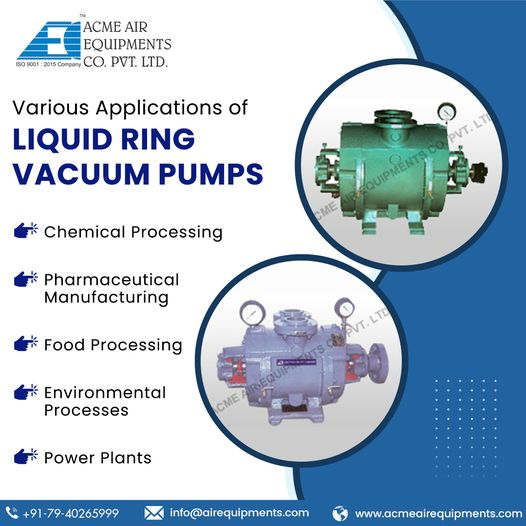
Stable Operation in High Vapor Conditions
Solvent recovery applications typically produce large volumes of vapor with variable loading. A key strength of dual stage vacuum technology is its ability to maintain performance under fluctuating vapor concentrations. The liquid ring design inherently manages vapor without mechanical contact, which reduces the risk of damage and enhances long-term reliability.
Even when solvent concentrations are high, a two stage liquid ring vacuum pump can operate without cavitation-a common risk in single-stage systems. This stability is especially beneficial in batch processes, where vapor load can spike unpredictably.
Process Integration: How These Pumps Fit into Solvent Recovery Systems?
In a typical solvent recovery system, a two stage vacuum pump is integrated just after the process chamber and upstream from the condenser. Its function is to create the pressure differential needed to draw vapors into the recovery line, pass them through the condenser and return the recovered solvent to storage.
The pump operates by using a service liquid-often water or a compatible process fluid-to form a rotating ring inside the pump chamber. The rotating impellers, set eccentrically within this ring, trap solvent vapors and compress them in two stages. This compression sequence ensures that the vapors are transported efficiently and that pressure remains consistent, even when process conditions fluctuate.
This dual impeller configuration is also key to managing heat load. During solvent recovery, thermal equilibrium can impact condensation rates. By maintaining a stable vacuum and low internal temperatures, these pumps support efficient heat transfer and solvent condensation downstream.
Design Considerations for Solvent Recovery Applications
Solvent recovery systems place unique demands on vacuum technology and two stage pumps are built with these considerations in mind:
- Corrosion Resistance: Solvents can be chemically aggressive. Most two stage pumps used in recovery systems feature corrosion-resistant materials such as stainless steel or specially coated surfaces to prevent degradation.
- Seal Integrity: Maintaining vacuum integrity is critical. These pumps use mechanical seals and precision-engineered shafts to eliminate leaks and ensure consistent operation during long recovery cycles.
- Liquid Compatibility: The sealant liquid used in the pump may interact with the solvent vapors. In such cases, the system must ensure compatibility or employ closed-loop recovery of the service fluid to prevent contamination.
- Thermal Management: Solvent vapor can introduce significant thermal energy into the system. Heat exchangers may be integrated with the pump to regulate the service liquid temperature, ensuring vapor condensation remains effective.
These design features make heavy-duty two stage vacuum pumps a trusted solution in facilities that require continuous solvent recovery without compromising system uptime or solvent purity
Industry Applications and Operational Benefits
Pharmaceuticals and Fine Chemicals
In pharmaceutical production, high-purity solvents must be recovered after drying and crystallization processes. Two stage liquid ring vacuum pumps are ideal for recovering these solvents without degradation or contamination, supporting regulatory compliance and cost control.
Chemical Manufacturing
Chemical plants use vast quantities of solvents in reaction and extraction processes. Recovery systems powered by two stage pumps reduce solvent loss, improve sustainability and lower operational expenses. These pumps are particularly useful in recovering azeotropic mixtures or solvents with complex vapor behaviors.
Industrial Coatings and Paints
In coatings manufacturing, solvents are used to dissolve binders and adjust viscosity. During application and drying, solvent vapors are captured using vacuum-assisted recovery systems. Two stage pumps ensure that valuable solvents are reclaimed efficiently, even in high-volume production environments.
Waste Minimization and Environmental Control
Many plants are now required to minimize volatile organic compound (VOC) emissions. Solvent recovery systems equipped with two stage liquid ring vacuum pumps enable facilities to reduce atmospheric release while meeting environmental standards. This not only benefits compliance efforts but also recycles material that would otherwise be wasted.
FAQs about Two Stage Liquid Ring Vacuum Pump
1. What is the role of a two stage liquid ring vacuum pump in solvent recovery?
It creates the deep vacuum needed to vaporize and transport solvents for efficient recovery and condensation.
2. Can these pumps handle different types of solvents?
Yes, they can manage a wide range of solvents including acetone, ethanol, methanol and more, as long as material compatibility is ensured.
3. Why are two stages better than one in solvent recovery?
Two-stage compression enables lower pressures and more efficient handling of high vapor loads, essential for complete solvent recovery.
4. Are two stage vacuum pumps energy-efficient?
They may be more energy-efficient in low-pressure operations due to reduced compression ratios in each stage.
5. What industries benefit most from this pump technology?
Pharmaceuticals, chemicals, coatings and any industry that uses or recycles solvents can benefit significantly from dual stage vacuum systems.
Conclusion
The integration of two stage liquid ring vacuum pumps in solvent recovery systems represents a significant advancement in vacuum technology for industrial processes. Their dual-stage compression capability provides the deep vacuum levels required for efficient solvent vaporization, while their robust design allows for continuous operation in vapor-rich and chemically aggressive environments.
By maximizing the recovery of solvents and minimizing losses, these pumps contribute to more operations, lower costs and improved process control. From pharmaceuticals to petrochemicals and beyond, industries are turning to dual stage vacuum pump technology as a cornerstone of modern solvent recovery systems.