Table of Contents
In modern industry, precision, efficiency and reliability are non-negotiable-especially in operations involving controlled environments and material handling. At the core of many such processes lies a critical yet often overlooked component: the vacuum pump. From creating a vacuum in packaging systems to enabling large-scale chemical distillation, vacuum pumps serve as a backbone for countless industrial operations.
This article explores the industrial applications of vacuum pumps, focusing on technologies like Liquid Ring Vacuum Pumps, Two-Stage Liquid Ring Vacuum Pumps, Water Ring Vacuum Pumps and Oil Sealed Vacuum Pumps. These systems are widely used in manufacturing, pharmaceuticals, food processing, chemical production and more. By understanding where and how vacuum pumps are applied, businesses can select the right technology to meet their operational needs efficiently.
Vacuum Pumps in Industrial Contexts
A vacuum pump is a mechanical device that removes air or gas molecules from a sealed volume to create a vacuum. This environment is essential for operations where air presence can interfere with processes, cause contamination or reduce efficiency.
Vacuum levels can range from rough to ultra-high vacuum, depending on the industrial requirement. Vacuum pumps are used not only for creating a vacuum but also for transferring materials, drying substances and facilitating gas phase transformations.
The industrial environment dictates which type of vacuum pump is appropriate, based on factors like gas composition, required vacuum depth, temperature and contamination risk.
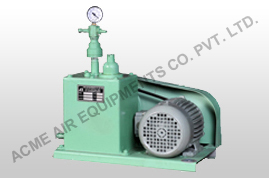
Liquid Ring Vacuum Pumps in the Chemical and Process Industries
Why Liquid Ring Technology is Essential?
Liquid Ring Vacuum Pumps operate using a rotating impeller inside a chamber filled partially with a sealing liquid (usually water or oil). The rotation forms a “liquid ring,” creating chambers that compress and expel gas. These pumps are best suited for handling wet gases, saturated vapors and condensable gases.
Key Industrial Applications
- Chemical Plants: Used in vacuum distillation, crystallization and solvent recovery.
- Petrochemicals: Efficient for vapor handling in flare gas recovery systems.
- Paper Industry: Removes moisture from pulp and paper webs in the drying phase.
- Textile Dyeing: Facilitates dye impregnation under vacuum conditions.
Liquid Ring Pumps are favored for their ability to handle corrosive gases and liquids without mechanical damage, making them indispensable in process industries.
Two-Stage Liquid Ring Vacuum Pumps for Deeper Vacuum Needs
Enhanced Performance in Critical Operations
A Two-Stage Liquid Ring Vacuum Pump features two impeller stages in series. This design allows the pump to achieve deeper vacuum levels than single-stage models, without compromising flow rate or stability. It’s a preferred option where lower absolute pressures are necessary.
Industrial Use Cases
- Pharmaceuticals: Supports vacuum drying of APIs and intermediates.
- Plastics Manufacturing: Maintains precise pressure for vacuum degassing in extrusion processes.
- Fertilizer Production: Assists in vacuum crystallization for nitrogen and phosphate-based products.
- Food Processing: Enables dehydration and low-temp cooking to preserve nutritional value.
Two-stage systems offer improved efficiency in high-demand applications with substantial vapor or gas loads, delivering energy savings and stable performance.
Water Ring Vacuum Pumps in Moisture-Rich and Harsh Environments
Cost-Effective and Durable
Water Ring Vacuum Pumps, a subcategory of liquid ring technology, use water exclusively as the sealant. They offer reliable performance in wet conditions and tolerate non-condensable gases and contaminated fluids better than many alternatives.
Common Applications
- Wastewater Treatment Plants: For aeration tank degassing and sludge drying.
- Mining and Mineral Processing: Used for dewatering operations.
- Cement Manufacturing: Removes trapped air in material mixing processes.
- Breweries and Distilleries: Assists in fermentation vessel degassing.
Water ring pumps are often chosen for their lower operating cost and the fact that water is readily available and environmentally neutral in many facilities.
Oil Sealed Vacuum Pumps for Precision and Cleanroom Operations
Optimal for High Precision Requirements
Oil Sealed Vacuum Pumps, particularly rotary vane designs, are ideal for dry and clean applications where air and moisture must be completely removed. These pumps rely on oil to seal, lubricate and cool the system, making them suitable for moderate to high vacuum levels.
Industrial Sectors Benefiting from Oil-Sealed Technology
- Semiconductor Fabrication: Maintains ultra-clean vacuum environments for chip etching.
- Medical Equipment Manufacturing: Enables vacuum forming and sterilization of components.
- Laboratories and R&D: Powers vacuum ovens, chambers and test rigs.
- Vacuum Packaging: Widely used in food and pharmaceutical packaging lines for air removal.
Though they require regular oil changes and maintenance, their reliability and vacuum consistency make them a staple in precision manufacturing.
Vacuum Pumps in Bulk Handling and Vacuum Unloading Systems
Material Transfer Under Vacuum
Industrial plants often use vacuum unloading systems to transport powders, grains or granules from containers, silos or trucks into processing equipment. These systems use negative pressure generated by vacuum pumps to move material without manual handling or spillage.
Industries Using Vacuum Unloading Technology
- Agricultural Processing: Moves grain, flour and feed ingredients.
- Plastics: Transfers plastic pellets to extrusion machines.
- Cement and Construction Materials: Handles fine powders in batching operations.
- Chemical Plants: Transfers raw or reactive powders under sealed conditions.
Vacuum systems offer a cleaner, safer alternative to mechanical conveyors, especially when dealing with volatile or hazardous materials.
Choosing the Right Vacuum Pump for Your Application
Selecting the appropriate vacuum pump involves understanding:
- Required vacuum depth (rough, medium or high vacuum)
- Gas characteristics (dry, wet, corrosive, particulate-laden)
- Continuous vs. batch operation
- System compatibility with upstream and downstream equipment
Working with knowledgeable vacuum system integrators ensures the correct sizing, materials and control systems are applied to meet both process and regulatory demands.
FAQs about Vacuum Pumps
1. What industries commonly use vacuum pumps?
Vacuum pumps are used in chemicals, pharmaceuticals, food processing, packaging, electronics, wastewater treatment and mining.
2. How does a liquid ring vacuum pump work?
It uses a rotating impeller inside a fluid-sealed chamber to trap and compress gas, ideal for wet and vapor-laden environments.
3. Why choose a Two-Stage Liquid Ring Vacuum Pump?
For applications requiring deeper vacuum levels and high gas loads, such as vacuum distillation or drying in chemical and pharma plants.
4. What are oil sealed vacuum pumps best suited for?
They’re used in clean, dry environments like labs, semiconductor fabs and packaging lines needing consistent vacuum performance.
5. Can vacuum pumps be used for material handling?
Yes, especially in vacuum unloading systems that move powders or granules in food, plastic, cement and chemical industries.
Conclusion
Vacuum pumps are vital to a vast array of industrial applications, from supporting chemical reactions and drying materials to transporting powders and packaging products. Whether it’s a Liquid Ring Vacuum Pump handling saturated vapors in a chemical plant, a Two-Stage system supporting pharmaceutical drying or an Oil Sealed Vacuum Pump ensuring precision in electronics manufacturing, the right pump delivers operational reliability and process efficiency.
As industries continue to advance, the role of vacuum technology only grows in importance. Understanding each type of vacuum pump and its ideal application can help businesses reduce energy use, improve productivity and maintain product quality across demanding environments.