Table of Contents
Vacuum pumps have become indispensable components in industrial processing across sectors such as pharmaceuticals, petrochemicals, food processing, metallurgy and electronics. Whether used for material handling, packaging, drying or chemical processing, the use of vacuum pumps has expanded significantly in both developing and developed economies. As a result, global demand and supply for various types of vacuum pumps, including liquid ring vacuum pumps, oil seal vacuum pumps and mechanical vacuum pumps, continue to evolve with technological progress and industrial needs.
This article provides an analytical look at the growing global demand and supply landscape for vacuum pumps. It also explores what drives demand in key countries such as Germany, the United States, Australia and France, while highlighting the industrial preferences for different vacuum pump systems.
What is a Vacuum Pump and How Does It Work?
A vacuum pump is a mechanical device that removes air or gases from a sealed chamber to create a partial vacuum. Depending on the operating principle, vacuum pumps are categorized into several types, each optimized for different pressure levels and gas compositions.
How Does it Work?
Vacuum pumps typically operate using either displacement or momentum transfer.
- Liquid ring vacuum pumps use a rotating impeller inside a liquid-sealed chamber to trap and compress gases.
- Oil seal vacuum pumps utilize rotary vanes lubricated by oil to remove air efficiently from a chamber.
- Mechanical vacuum pumps, including piston and screw types, are preferred for dry applications with clean gases.
Global Demand Drivers for Vacuum Pump Systems
Germany: Engineering Precision and High-Tech Manufacturing
Germany remains a leader in mechanical engineering and process manufacturing. The demand for mechanical vacuum pumps and oil seal vacuum pumps is significant in German industries focused on research laboratories, pharmaceuticals and specialty chemicals. Manufacturers also contribute to global exports of high-end vacuum pump systems, especially vacuum unloading systems and Two Stage Liquid Ring Vacuum Pumps for solvent recovery and distillation.
United States: Broad Industrial Adoption and Innovation
The U.S. market is highly diversified, with strong demand in semiconductors, aerospace, biotech and energy. Vacuum pump demand is driven by high-throughput requirements and environmental controls, especially in vacuum-assisted chemical processing and cleanroom applications.
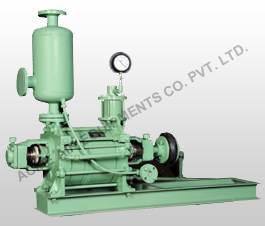
The U.S. sees strong uptake of liquid ring vacuum pumps, which offer high reliability in corrosive and vapor-rich environments.
Australia: Mining and Environmental Applications
Australia’s industrial vacuum pump demand is largely driven by its mining, metallurgy and wastewater treatment sectors. The need for robust and moisture-tolerant water ring vacuum pumps is prominent. Australian industries often operate in rugged conditions, requiring durable equipment that supports long operational cycles with minimal downtime.
France: Pharmaceuticals and Fine Chemicals
France’s pharmaceutical and cosmetic sectors heavily utilize vacuum pump systems for distillation, crystallization and freeze-drying. The use of Two Stage Liquid Ring Vacuum Pumps is high in cleanroom and controlled-environment manufacturing. French demand is also shaped by stringent environmental and safety regulations, which promote closed-loop vacuum unloading systems.
Supply Trends and Manufacturing Ecosystem
Global Supply Concentration
The vacuum pump market is supported by a mix of global players and regional manufacturers. Liquid ring vacuum pumps manufacturers from Germany, China and India lead in producing cost-effective, high-performance solutions. Meanwhile, manufacturers in the U.S. and Europe dominate high-end segments such as vacuum systems for hazardous chemical environments.
OEM Integration and Custom Systems
A growing trend is the integration of vacuum pumps into OEM systems for turnkey solutions. Process plant builders are increasingly sourcing custom vacuum pump systems to fit specific material, temperature and pressure conditions. This has spurred demand for modular and configurable pump designs.
Technological Advancements in Supply
Key innovations affecting the supply side include:
- Dry-running vacuum pumps that eliminate oil contamination risks.
- Smart vacuum pump systems with integrated sensors and PLCs for automated control.
- Corrosion-resistant pump designs for aggressive chemical environments.
These enhancements allow vacuum pump uses to expand into more delicate and demanding industrial operations.
Industrial Applications and Their Influence on Vacuum Pump Types
Liquid Ring Vacuum Pumps in Chemical and Power Plants
Used primarily in chemical, pharmaceutical and energy sectors, liquid ring vacuum pumps handle saturated gases and vapors with high efficiency. They are preferred in:
- Solvent recovery
- Vacuum filtration
- Degassing systems
- Vacuum unloading systems in tank terminals
Their tolerance for wet gases makes them indispensable in environments where conventional pumps may cavitate or fail.
Two Stage Liquid Ring Vacuum Pump for High-Vacuum Demand
For industries requiring deeper vacuum levels without oil contamination-like in petrochemicals and plastics-Two Stage Liquid Ring Vacuum Pumps offer performance advantages. These pumps can operate continuously under heavy vapor loads, making them ideal for vacuum distillation and evaporation systems.
Water Ring Vacuum Pumps in Bulk Handling
Water ring vacuum pumps, a variant of liquid ring technology, are widely adopted in food processing, ceramics and wastewater treatment. Their ability to work with easily available water as the sealant fluid makes them cost-effective for many mid-range vacuum applications.
Oil Seal Vacuum Pumps in Precision Processes
Oil seal vacuum pumps remain the top choice in clean environments such as semiconductor fabrication, lab-scale processes and fine chemical production. Applications include:
- Freeze-drying
- Vacuum packaging
- Laboratory vacuum ovens
They provide consistent vacuum with excellent pressure control, suitable for applications that demand low vapor pressure and precise results.
Market Forecast and Future Demand Outlook
The global vacuum pump market is expected to grow steadily over the next decade. This demand is underpinned by:
- Increased automation and process control in manufacturing.
- Environmental compliance pressures in chemical processing.
- Expansion of electronics, pharmaceuticals and biotechnology.
- Growth in clean energy and carbon capture projects.
Regions such as Southeast Asia, South America and Eastern Europe are also showing rising demand for entry-level vacuum pump systems and vacuum unloading systems for use in fertilizer, cement and mining sectors.
FAQs about Vacuum Pump
1. What is a vacuum pump used for in industry?
Vacuum pumps are used to remove gases from sealed systems for processes like drying, packaging, distillation and material conveying.
2. Which type of vacuum pump is best for wet gas applications?
Liquid ring vacuum pumps are ideal for saturated gases and moist environments, common in chemical and energy sectors.
3. What is the advantage of a Two Stage Liquid Ring Vacuum Pump?
It delivers deeper vacuum levels with higher throughput, suitable for solvent recovery and vacuum distillation.
4. How does an oil seal vacuum pump work?
It uses oil as a sealant and lubricant to evacuate air from a system, offering consistent performance in clean applications.
5. What industries use vacuum unloading systems?
They are used in fertilizer, cement, pharmaceutical and food industries for bulk powder and granular material transfer.
Conclusion
The global market for vacuum pumps is marked by consistent growth, technical innovation and evolving application requirements. From liquid ring vacuum pumps in chemical plants to oil seal vacuum pumps in pharmaceutical labs, each pump type serves a unique set of functions across industries.
Understanding the regional demand variations, supply dynamics and application-specific needs is essential for stakeholders-from plant engineers to procurement teams and equipment manufacturers. As technologies continue to evolve and industries scale, the role of efficient, tailored vacuum pump systems becomes increasingly central to industrial productivity and operational safety.