Table of Contents
Introduction
Welcome to the world of Mechanical Vacuum Boosters, where innovation meets efficiency in re-used oil distillation. This article delves into the intricacies of these boosters, offering insights into their design, applications, and the transformative impact they have on various industries.
Twin Lobe Boosters: A Varied Design Approach
Mechanical Vacuum Boosters come in a variety of designs, with the Twin Lobe Booster leading the pack. Whether air-cooled or water-cooled, these boosters are engineered to handle vapours and gases with lower specific power consumption, ensuring efficiency without compromising performance.
Specific Power Consumption: The Key Advantage
One of the standout features of these boosters is their ability to operate at lower specific power consumption. This advantage translates into energy efficiency, making them an ideal choice for industries seeking sustainable solutions.
Handling Vapours and Gases: Precision at its Best
The precise and constant volume displacement at rated conditions sets Mechanical Vacuum Boosters apart. This characteristic makes them well-suited for applications where accuracy is paramount, such as in handling Thionyl Vapours.
Industries and Thionyl Vapors: Tailored Solutions
Industries requiring the handling of Thionyl Vapors find comfort in the compatibility and design of vacuum systems provided. These systems are crafted to thrive in acidic environments, offering tailored solutions to meet the unique needs of each customer’s processes.
Solvent Recovery vs. Raw Material Substitution
In the quest to reduce costs and waste, many industries face the dilemma of choosing between solvent recovery and raw material substitution. This section explores the merits of in-process solvent recovery utilizing vacuum technology as a more economically preferable alternative.
In-Process Solvent Recovery: A Cost-Effective Mechanism
Discover the economic advantages of utilizing solvent vapor recovery equipment, incorporating vacuum pumps and condensate receivers. This approach proves to be not only cost-effective but also environmentally conscious, presenting a compelling case against raw material substitution.
Complete System Design: Booster at the Core
Unveiling the heart of the system, the Booster takes center stage. Learn how it seamlessly integrates with primary pumps, condensers, valves, filters, drives, and instrumentation to function optimally in various modes. This holistic approach covers a broad vacuum spectrum, ranging from 10 to 10-3 mbar.
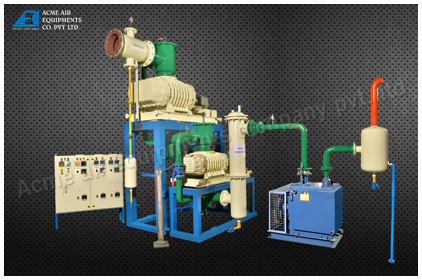
Wide Spectrum of Vacuum: 10 to 10-3 mbar
Explore the versatility of Mechanical Vacuum Boosters as they cover a wide spectrum of vacuum, ensuring adaptability to diverse industrial requirements. This section delves into the intricacies of maintaining pressure differentials between 50 to 100 mbar and achieving optimal pressure ratios.
Versatile Combinations and Stages
Dive into the world of versatility as we discuss the design and execution of a broad range of combinations and stages. With a maximum pumping speed of up to 200,000 LPM, these boosters prove their adaptability across various industrial processes.
Pressure Maintenance: The Critical Differential
Understanding the critical role of pressure maintenance, this section sheds light on how Mechanical Vacuum Boosters achieve and maintain pressure differentials crucial for their efficient operation. The emphasis is on optimal performance and reliability.
Integration with Primary Pumps
Learn about the seamless integration of the system by utilizing Two Stage Liquid Ring Pump, Oil Sealed Vacuum Pump, Rotary Dry Vacuum Pump, or Steam/Water Jet Ejector as the primary pump. This strategic integration ensures a comprehensive and effective vacuum solution.
Applications Across Industries: A Diverse Range
Explore the myriad applications of Mechanical Vacuum Boosters across industries. From distillation and degassing to coating, refining of industrial oil, vacuum impregnation, semiconductor processing, separation of fluids, space simulation, to vacuum freeze drying – these boosters prove indispensable.
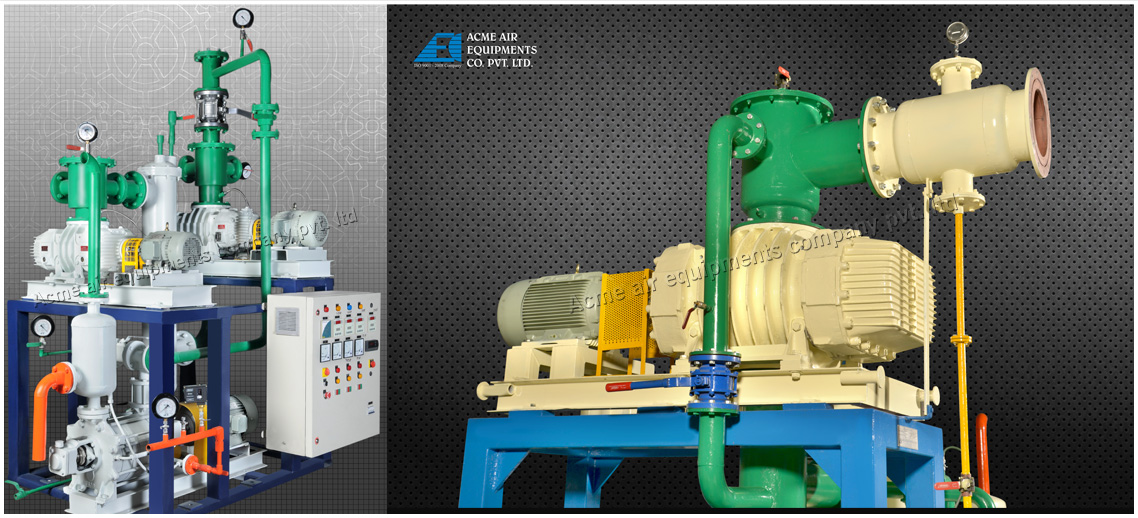
Chemical, Pharmaceutical, and Metal Powders: Common Users
Delve into specific industries such as chemical, pharmaceutical, metal powders, flavor and fragrance, and PET solid-state manufacturing that extensively benefit from the application of solvent recovery vacuum systems.
Conclusion
In conclusion, Mechanical Vacuum Boosters emerge as game-changers in the landscape of industrial vacuum systems. Their versatility, efficiency, and tailored solutions position them as the preferred choice for industries seeking excellence in distillation, degassing, and various other processes.